Проект
создание технологического центра разработки
и отладки технологического оборудования для получения наноматериалов в соответствие с патентом WO2013009220.
Ведение
Цель проекта - внедрение в производство уникальной технологии разделения порошковых материалов по плотности и размерам частиц.
Для достижения цели предлагается организовать на базе предприятия VectorNPT, команду сотрудников, которая будет заниматься маркетинговыми исследованиями и конструкторскими разработками.
Также предлагается создать экспериментальное производство, задачей которого является:
- Разработка и согласование с инвесторами подробного бизнес-плана на создание высокотехнологичного производства по любому направлению, где может использоваться предлагаемая технология.>
- Разработка нормативно техническая и конструкторской документации на изготовление оборудования будущего производства.
- Разработка проекта автоматического управления технологическим процессом.
- Подготовка помещения для производства.
- Сборка оборудования на территории экспериментального производства из изготовленных узлов. Запуск оборудования, его тестирование и наладка. Подтверждение заявленных параметров.
- Поиск источников сырья, в соответствии с предъявляемыми требованиями к качеству.
- Уточнение видов выпускаемой продукции по качественным и количественным характеристикам.
- Заключение контрактов на поставку продукции или передача оборудования заказчику для реализации собственных проектов.
Концепция идеи
В настоящее время в мировой индустрии, наблюдается тенденция увеличения потребности высокотехнологичных производств в особо чистых нано и микропорошках различных материалов.
Такие отрасли промышленности, как микроэлектроника, керамика, производство огнеупорных и антифрикционных материалов, производство порошковых металлов, наращивают свои мощности по потреблению таких материалов и выпуску новой продукции на их основе.
В настоящее время 80% мирового производства светодиодных излучающих элементов производятся на подложках из особо чистого карбида кремния.
Огнеупорные материалы, изготовленные из особо чистых наноматериалов, имеют срок эксплуатации в несколько раз выше, чем изготовленные из обычных.
Керамические изделия, изготовленные из наноматериалов, имеют технологические параметры в несколько раз выше, чем из обычных материалов.
Микрочипы, изготовленные из особо чистого карбида кремня, работают при температуре до 650 С (против 120 С, изготовленных из чистого кремния).
Единственное, что сдерживает рост применения наноматериалов это их высокая цена и незначительный объем производства, не удовлетворяющие потребности современной индустрии.
Внедрение новой технологии получения нанопорошковых материалов, позволит удовлетворить потребности рынка в этих материалах и значительно снизить их стоимость (в 10..20 раз. Это даст толчок в развитии всей индустрии, базирующейся на использовании этих материала.
Краткое описание технологии
Предлагаемая технология размерной классификации порошков является усовершенствованным продолжением аналогичной технологии, разработанной в начале 90 –х годов и запатентованной в 1997 году.
Принцип работы технологии основан на управляемом течении жидкости содержащей частицы вещества (суспензии), которые надо разделить на фракции.
С этой целью было сконструировано специальное устройство (головка), которая устанавливается в ротор, вращающийся со скоростью до 20000 об/мин.
Геометрически, устройство представляет собой тор. В устройстве, перпендикулярно оси вращения сделан цилиндрический канал, соединяющий наружную и внутреннюю поверхность тора. Наружная поверхность тора закрыта заглушкой с отверстием диаметром от 0.3 до 0.8 мм (форсунка). Во вращающийся вокруг оси тор, в среднюю часть канала подается жидкость, содержащая частицы вещества концентрацией до 300% кг/дм3. Объем жидкости подаваемый в среднюю часть канала превосходит объем жидкости выходящей, за счет действия центробежных сил, из канала через форсунку. Избыточная часть жидкости вытекает из канала во внутреннюю часть тора, при этом она течет против действия центробежных сил.
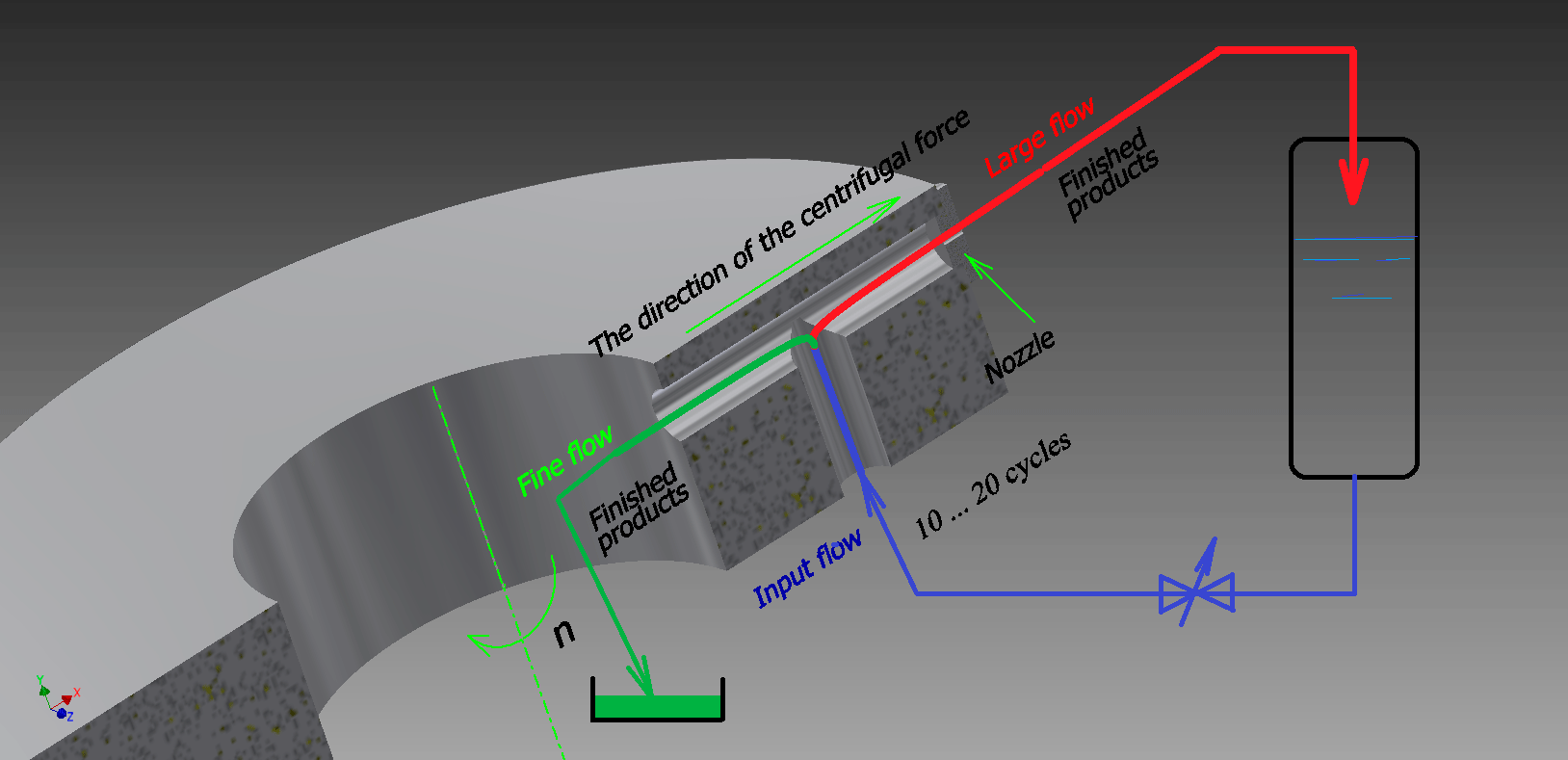
На этом участке канала и происходит разделение частиц порошка по размерам, так как на каждую частицу действует две противоположно направленные силы: -центробежная сила, действующая против потока, направленная от оси вращения ротора в сторону форсунки и сила сопротивления жидкости, действующая противоположно направлению центробежной силе.
Для крупных частиц центробежная сила превышает силу сопротивления жидкости и такие частицы движутся против потока в сторону форсунки и выходят за пределы устройства. Для мелких частиц сила сопротивления жидкости превышает центробежную силу, и они двигаются вместе с потоком против центробежной силы и выносятся потоком жидкости во внутрь устройства.
Диаметр частиц, при котором обе силы равны (зона разделения), зависит от вязкости, плотности жидкости, плотности частиц, скорости вращения устройства, его геометрических размеров и скоростей потоков жидкости. Изменяя эти параметры, можно регулировать зону разделения от 0.1 микрона до 20 микрон.
По данной технологии было разработано промышленное оборудование для высококачественной размерной классификации абразивных алмазных порошков. Качество разделения частиц по размерам превышало установленные стандарты для этой отрасли.
За 15 лет работы производства отработаны технологические режимы работы и конструкции устройств разделения для разных материалов таких как алмаз, карбид кремния, карбид вольфрама, дисульфид вольфрама, угольные частицы, глинистые руды с содержанием благородных металлов и др. вещества.
Для каждого вещества подобраны типы и концентрации поверхностно активных веществ, предотвращающих слипание частиц в жидкости (антикоагулянты).
Недостатком технологии 97 года является то, что входной поток, попадая в горизонтальный канал, разделяется на два противоположных потока. Один поток движется внутрь устройства по каналу противоположно направлению действия центробежных сил. В этом потоке происходит разделение частиц по размерам. Другой поток движется в сторону форсунки в направлении действия центробежных сил. В этом потоке разделение частиц не происходит.
Для полного разделения частиц на две фракции необходимо поток выходящий через форсунку снова подавать на вход устройства. Через 10 … 20 циклов частицы полностью разделяются на две фракции. В связи с этим процесс может проходить только с ограниченным объемом жидкости, которая зацикливается по потокам и процесс длится до полного разделения. В существующем производстве объем жидкости составлял 20 дм.куб. и процесс разделения длился от 3 до 6 часов в зависимости от размера зоны разделения. Количество готового продукта составляло 5..6 кг.
Для увеличения производительности разделения в 2011 году была запатентована технология, которая позволяет разделять частицы по размерам за один проход жидкости, то есть без замыкания потоков.
Производительность такой технологии зависит от геометрических параметров устройства и соответственно объемных величин потоков.
Выход готового продукта с одной установки составляет 540 кг/час и более для фракции -10 микрон.
Области применения технологии
- Производство компонентов для изготовления высокопрочного водонепроницаемого бетона. Такой бетон получается из обычного бетона путем добавления мелкодисперсных порошков фракций от 0,5…10 микрон, в количестве от 1 до 3% на тонну бетона. В настоящее время высокая цена и отсутствие в достаточном количестве таких фракций порошков сдерживает рост производства высокопрочного бетона и соответственно всех направлений строительной. Из такого бетона могут изготавливаться детали и узлы объектов машиностроения. Например, станины для тяжелых карусельных станков и прессов, которые в настоящее время отливаются из специального чугуна. Применение высокопрочного бетона, позволит сократить время изготовления таких узлов и снизить их конечную стоимость. Из такого бетона могут изготавливаться корпуса редукторов и других подобных изделий. Особенно незаменим такой бетон в строительстве портовых сооружений - от строительства причальных линий до высокопрочных дорожных покрытий, по которым перемещается специальная тяжелая техника. Возможно, получения вспененных бетонов по прочности, не уступающие обычным тяжелым бетонам.
- Производство порошковых компонентов для изготовления высокотехнологичной керамики военного и конструктивного назначения (броневая керамика, керамика для ядерного топлива (ТВЭЛ) и прочее). Для производства такой керамики требуются порошковые компоненты с размером частиц не более 0,4 микрона. Отсутствие таких порошковых компонентов в достаточном количестве и их высокая цена сдерживают рост производства в этой области промышленности.
- Производство мелкодисперсных порошков фракций 0-0,1 микрона антифрикционных материалов, таких как дисульфид вольфрама, дисульфид молибдена, гексагональный нитрид бора. Такие порошки добавляется в обычные технические масла, что значительно увеличивает их трибологические свойства. Если такой порошок добавить в традиционные смазочно-охлаждающие жидкости в количестве до 5%, то стойкость режущего инструмента и скорость резки возрастает на 35..45%.
- Производство водоугольного топлива для замены дизельного топлива в котлах отопления помещений. Незначительная по стоимости переделка узлов впрыска традиционных котлов отопления позволит использовать вместо дизельного топлива - водоугольное, что значительно снизит эксплуатационные затраты такого оборудования. В настоящее время водоугольное топливо состоит из воды и угля с размером частиц менее 75 микрон. Применение новой технологии позволит получать такое топливо с размерами частиц менее 0.5 микрон, что позволит его использовать в качестве дизельного топлива для двигателей внутреннего сгорания. Водоугольное топливо дешевле углеводородного. По экологии оно занимает второе место после газа. По предлагаемой технологии можно удалять из водоугольного топлива зольные вещества механическим способом (Их содержание варьируется от 3% до 30%), что позволит использовать бурые угли. Основной недостаток водоугольного топлива на сегодняшний день, это небольшое время хранения до 7 дней, так как оно состоит из крупных частиц размером до 75 микрон. Использование предлагаемой технологии позволит получать топливо с неограниченным сроком хранения.
- Предлагаемая технология может быть использована для получения в промышленных объемах особо чистого кварцевого песка с размером частиц 0.5 микрон, который может быть использован для производства порошков карбида кремния полупроводникового качества, которые, в свою очередь, являются сырьем для производства полупроводниковых пластин , для электронной промышленности. Особо чистый порошок карбида кремния полупроводникового качества, также является сырьем для выращивания муассонита , не уступающего по своим ювелирным свойствам алмазу. Полупроводниковый карбид кремния в будущем полностью вытеснит чистый кремний из электронной промышленности.
- Предлагаемая технология может быть использована для выделения благородных металлов из руд в которых они содержатся в мелкодисперсном виде. Например существуют месторождения глинистых отложений в руслах рек, содержащие частицы платины размером 3..6 микрон в количестве 2…5 грамм на тонну руды. Не существует способов рентабельного промышленного выделения таких частиц, кроме использования предложенной технологии, которая позволяет выделять в час до 100 грамм платины.
- Предлагаемая технология может быть использована для промышленного обогащения руд. В частности, для некоторых типов производства титана и диоксида титана необходима руда с размером частиц не более 10 микрон и не менее 1 микрона. Так как более крупная фракция руды слишком медленно реагирует с реактивами при химическом обогащении , а частицы меньше 1 микрона слишком быстро реагируют с химикатами, что приводит к неуправляемому химическому процессу. Технология позволяет сконструировать аппараты механического обогащения производительностью до 20 тонн в час на одной установке.
- Предлагаемая технология может быть использована для получения нано размерных красок (с размером частиц менее 0,5 микрон). Такие краски обладают повышенной адгезией и белизной (максимальной белизной обладают краски с размерами частиц (0.1 – 0.5 микрон). Рекомендуемая область применения - авиация и судостроение.
- Предлагаемая технология может быть использована для получения порошков металлов в порошковой металлургии. Тугоплавкие металлы, такие как например, карбид вольфрама, получают спеканием порошков. Для спекания требуется различные фракции порошков с целью получения максимальной плотности упаковки шихты, и чем мельче порошки, тем более высокого качества можно получить материал. Работы в этой области показали, что можно выделять порошки карбида вольфрама размером 50 нанометров в промышленных объемах.
Это далеко не полный перечень областей промышленности, где может использоваться новая технология. Основная цель предлагаемой технологии, это снижение стоимости получения мелкодисперсных порошков в десятки раз, по сравнению с традиционными технологиями размерной классификации.Это позволит более успешно развиваться индустрии производства новых высокотехнологичных материалов.
Особенности технологии
Непрерывный процесс выделения материала, позволяет перенести технологию из разряда лабораторных к разряду промышленных.
Выделение происходит в жидкой среде, что позволяет перерабатывать токсичные вещества и не загрязнять атмосферу продуктами переработки.
Слабое место в технологии.
Слабым местом в технологии является ротор, вращающийся в опорах, с частотой вращения выше третьей критической скорости (выше 6000 об/мин). В связи с этим при конструировании и расчете необходимо обеспечить переход через зоны трех критических скоростей с малыми резонансными амплитудами и виброперегрузками.
В настоящее время теоретически развит и практически применен путь конструирования высокооборотных роторов, который не накладывает никаких ограничений на конструкцию и размеры ротора, сохраняет без изменения все его параметры, выбранные из оптимальных условий эксплуатации, технологии изготовления и прочности. Легкий переход через критические скорости достигается установкой ротора в упругие податливые опоры. В нашем случае используется схема установки ротора в шарнирную и упругую опору. Для каждого типа ротора требуется разработка собственной упругой опоры.
Для увеличения надежности работы и срока эксплуатации целесообразно заменить обычные опоры (на подшипниках качения) на магнитные. Такая замена требует отладки опытных образцов оборудования в лабораторных условиях, так как проектируемое оборудование не имеет близких аналогов.
Обоснование концепции создания опытного производственного участка.
Опытно производственный участок необходим для сборки и отладки изготовленного оборудования, технологических режимов и систем контроля и управления, перед тем как оно будет передано заказчику.
Для изготовления оборудования необходимо адаптировать конструкторскую документацию под требования изготовителей, наладить производственные отношения разработчик-изготовитель, которые неизбежно образуются в процессе создания изделия.
В процессе изготовления оборудования потребуется решать вопросы с технологами и материаловедами. Возможно потребуется произвести изменения в конструкции некоторых узлов оборудования с целью адаптации под требования местного производства.
Далее необходимо провести тестовые отладочные испытания разработанного оборудования на опытном участке, укомплектованном всей необходимой инфраструктурой (линия подготовки деионизованной воды, участок мелкого ремонта, электросиловые линии, водные и сливные коммуникации, и т.д.)
Предлагается создать производственный участок, который будет выполнять не только функции отладки нового разработанного оборудования , но и производящего продукцию, которая позволит существовать участку на самоокупаемости.
Ниже предлагаются варианты производственного участка с различными объемами инвестирования.